車の最新技術
更新日:2022.04.14 / 掲載日:2022.04.09
日産が発表した全固体電池を解説する【石井昌道の自動車テクノロジー最前線】
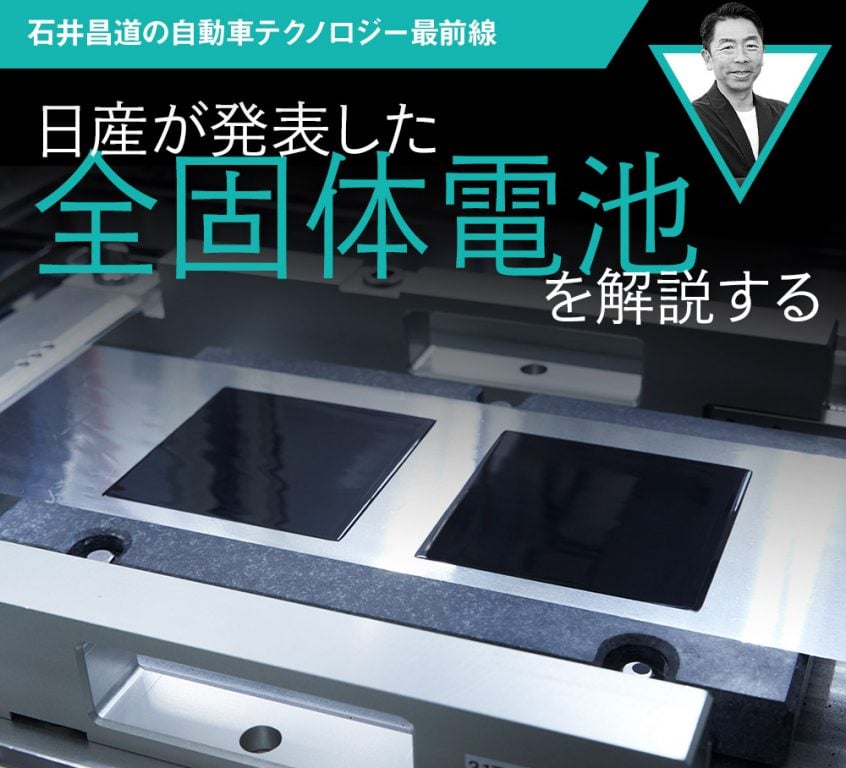
日産は2021年11月に長期ビジョンのNissan Ambition 2030を発表。今後5年間で2兆円を投資して電動化を加速、2030年度までにBEV15車種を含む23車種の新型電動車を投入するとともにグローバルでBEVの販売比率を50%以上に拡大するとしている。さらに、革新的な全固体電池を2028年度に市場投入するという野心的な目標も表明した。
現在のBEVの多くが採用するリチウムイオン電池は、正極と負極、およびそれを分けるセパレーター、そしてそれらの間を埋める電解質に液体の有機溶剤を使うという構成だ。正極と負極に蓄えたリチウムイオンが電解液を移動することで、充放電がなされる。正極、負極、電解液に使う材料によって性能が異なってくるが、高性能でポピュラーなのが正極にニッケル、マンガン、コバルトを使う3元系と呼ばれるもの。その割合もNMC622やNMC811などとかえることで進化してきたが、すでに性能の限界は見えてきている。
バッテリーの性能を表す指標の一つとして用いられる重量あたりのエネルギー密度は、初期のBEV用だったNMC111で100~140Wh/kg程度、NMC622で250~280Wh/kg程度、最新のNMC811で300Wh/kg程度、リチウムリッチにするなどもう少し進化させても350Wh/kg程度が限界だと言われている。とすれば、現在販売されているBEVに対して、多くても25%程度の進化しか見込めない。現在のBEVで航続距離が長いモデルは600km程度でバッテリー容量は100kWh級、車両重量は2~2,5tと重く電費には良くないというジレンマもある。航続距離は600kmでもエンジン車やハイブリッドカー並とは言えず、また大容量バッテリーは充電に時間もかかるのが課題だ。
そこでバッテリーのブレークスルーと期待されているポスト・液体リチウムイオン電池が全固体電池ということになる。重量あたりのエネルギー密度は350Wh/kgから上手くいけば500Wh/kg程度まで伸ばすことができるようだ。
エネルギー密度だけで見れば、液体リチウムイオン電池に対して劇的な進化とまでは言えないかもしれないが、それでもBEVとしては大きく進化し、エンジン車やハイブリッドカーと使い勝手で肩を並べる真のゲームチェンジャーになりうるポテンシャルがある。
というのも液体リチウムイオン電池は、電解質が液体のため高温で性能が落ちる、液漏れで発熱するリスクがあるというデメリットを抱えている。そのため、冷却装置や安全対策などに多くの技術が使われ、重量増、容積増、コスト増、エネルギーロスに繋がってしまっているのが現状だ。一般的に液体リチウムイオン電池は人肌程度の温度がもっとも調子が良く、動作範囲は20~60℃程度、できれば45℃を上回らない範囲で使いたいといったところのようだ。連続して高負荷をかけた走行や急速充電などでは発熱しやすく、きちんと冷却してあげないと簡単に上限温度に達する。
全固体電池は100℃近くまで許容するという。液体リチウムイオン電池を急速充電すると冷却することが求められ、SOC上限は70%程度に制限されるが、全固体電池ならば満充電までいけて、しかも素早い。350kWの充電器ならば15分しかかからないそうだ。また、安全対策も液体リチウムイオンに比べれば簡易化できる。
もう一つのメリットが電極に使用する材料の制約が大幅に緩和されることだ。液体リチウムイオンは性能低下を引き起こす副反応によって、正極材はニッケル、マンガン、コバルト、モリブデンなどといったレアアースを使う必要があったが、全固体電池は副反応が少ないために多くの選択肢が得られる。レアアースはコストがかかる上に供給にも不安があるが、それから開放される可能性が高い。正極はコストをミニマム化し、負極はリチウムリッチにしてエネルギー密度を最大化するのが日産の考え方だという。現在の液体リチウムイオンに対して、エネルギー密度は2倍、充電時間は1/3と大幅に性能向上。コストも下がる見込みで2028年時は75米ドル/kWh程度だという。エンジン車と同レベルになるのは65米ドル/kWhであり、それもスコープには入っているようだ。
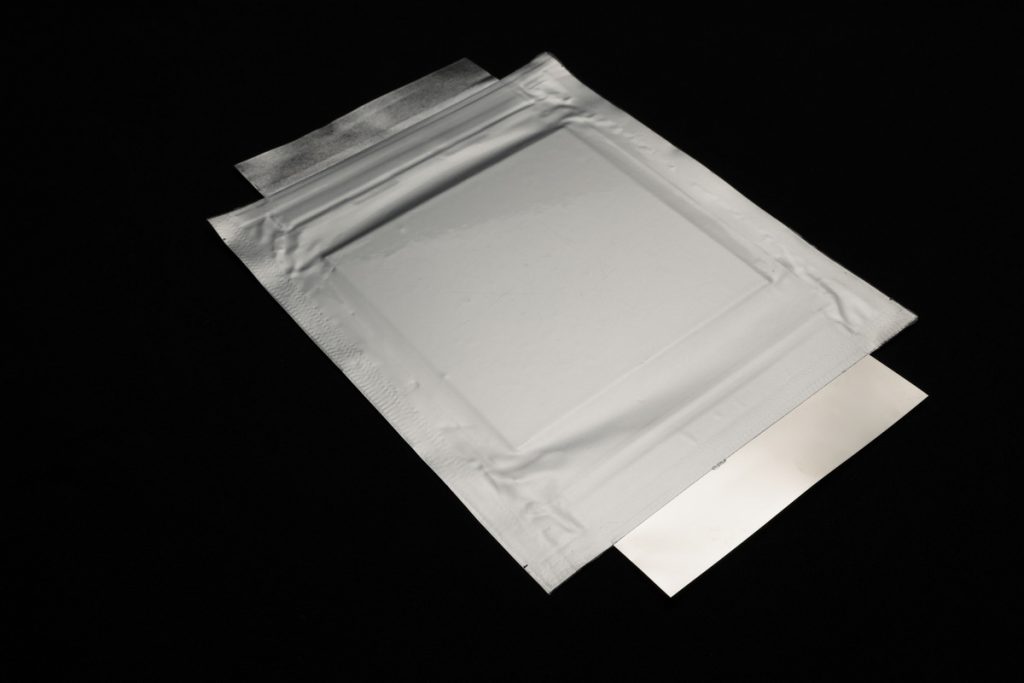
その一方で全固体電池の開発には課題もある。全固体電池もリチウムイオン電池の一種であり、電解質が液体から固体に置き換えられたもの。リチウムイオンが正極と負極を移動して充放電する仕組みにかわりなく、性能はその移動の早さなどに依存するが、肝心のリチウムイオンの伝導度が低いというのが弱点だ。液体ならば正極・負極材に電解質が浸透するので界面(物質の境目)が自然と安定しているが、固体では高密度で均一な界面の形成・維持が難しい。生産時には均一に混ぜらることができることも求められる。その条件を満たす材料選択が重要になる。材料の候補は多岐にわたっているので高度な計算科学、材料科学、解析・分析が必要であり日米の大学やNASAなどと協力して開発を進めているという。
これまでの開発でブレークするした例として6つがあげられた。
正極材料・構造では、正極活物質を接合するバインダーを、従来は活物質をべったりと覆うかっこうだったが網の目のような繊維状とすることでセル抵抗を大幅に低減した。リチウムイオン伝導度を高めることに繋がるのだ。
正極活物質と固体電解質の精密混合プロセスでは、凝集しにくい材料選びや活物質のコーティング、混ぜるスピードや温度の適正化などで均一・高密度混合が可能になった。繊維状のバインダーとの組み合わせで、セル抵抗は従来プロセスの1/10になった。
先端計算科学の科学およびネットワークは、膨大な材料候補(日産、NASAの共同研究による材料データベースは13万1000)から世界トップの科学者、計算環境下でAIなどを駆使。従来に比べると研究期間が1/2~1/5に短縮できるという。電気的・力学・化学・電気化学因子を同時に成立させる設計領域を導き、最適な材料を選定してくのが狙いだ。
材料コーティングでは充放電の繰り返しによって界面劣化が起きてリチウムイオン伝導性が悪化し、性能が下がっていくが、それを防ぐものだ。イオン伝導を妨げずに活物質の変質を抑えるのがポイントとなる。
層間の界面コントロールはリチウムイオンのデンドライト(析出)生成を抑える材料を採用し、特殊な物質で構成される保護層を形成する。短絡や性能劣化の原因となる負極場のリチウムイオン・デンドライトを抑制する取り組みだ。
界面の安定維持は、充放電の繰り返しによる性能劣化防止の取り組みで、ミクロ的にもマクロ的にも均圧設計とするとともに、充放電時の活物質の膨張・収縮を吸収するという。界面を密着させるのが全固体電池で難しいと言われるが、拘束面圧制御が大切であるようだ。
材料の選定、性能を引き出す、精度の管理などが要素技術であり、それぞれブレークスルーを目指して研究・開発が進んでいるのだ。
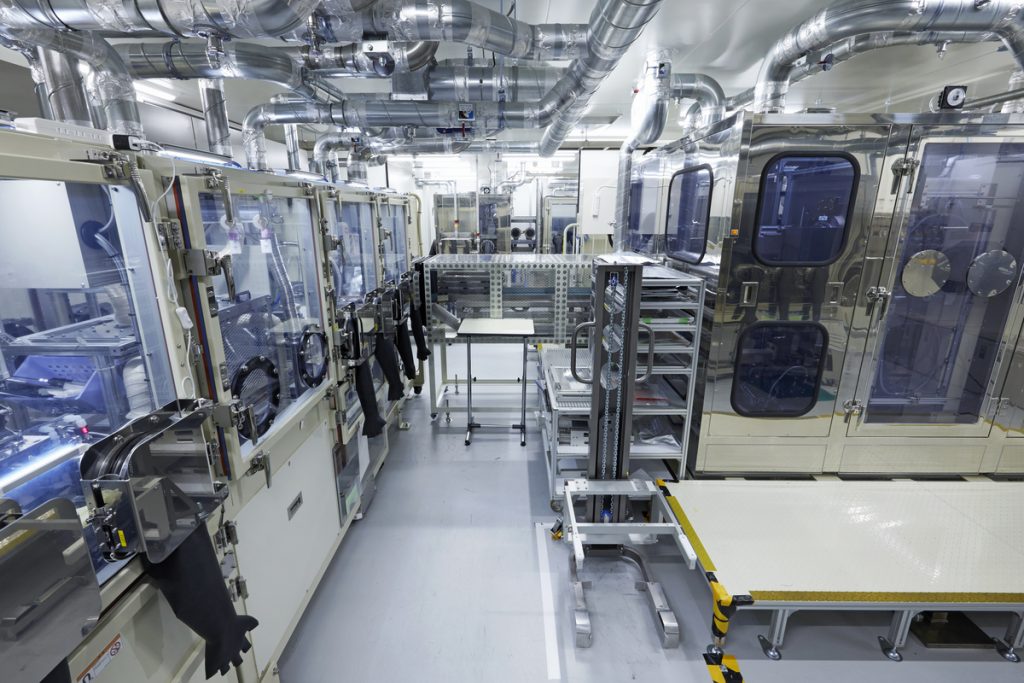
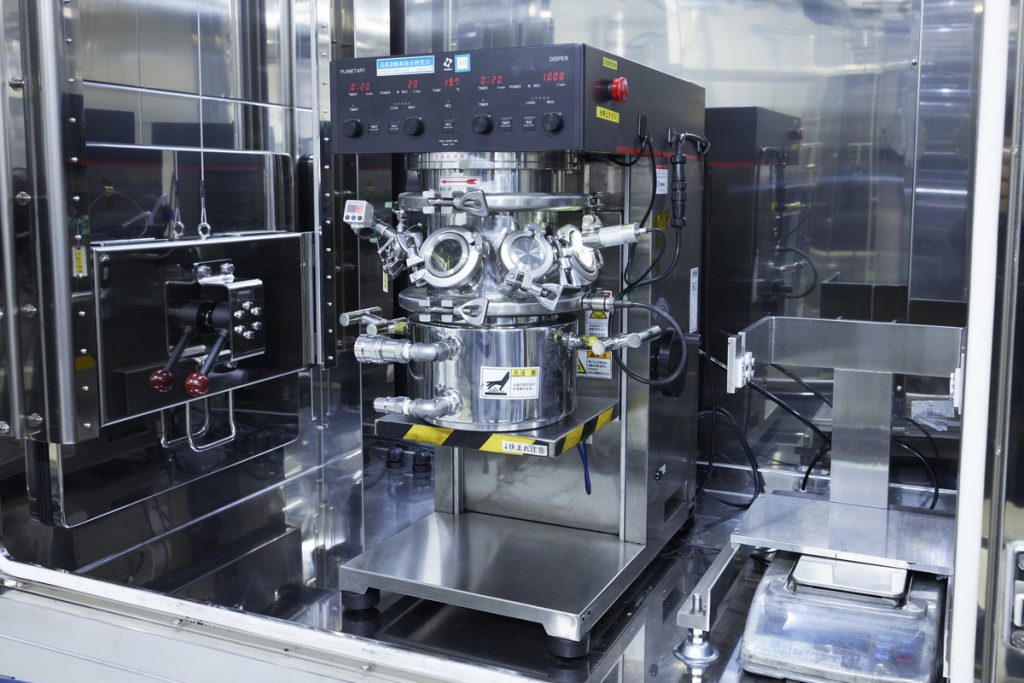
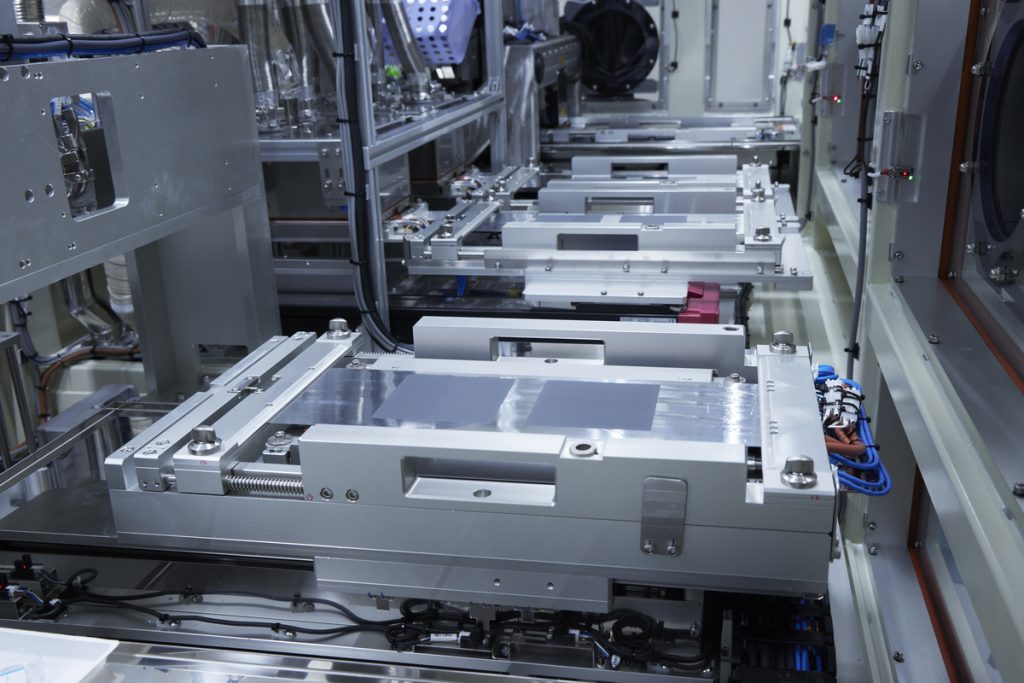
現在は研究・開発の段階だが、2024年にはパイロットプラントを立ち上げ、2028年の量産化に繋げていくというのがロードマップ。ハイブリッド等の小さなバッテリーではなく、また半固体などといわれるポリマー系でもない、真の全固体電池のBEVで本格的なゲームチェンジャーを狙っているという。全固体電池の開発競争は熾烈を極めているが、日産がリードカンパニーとなるかどうか、6年ほどで回答が見えてくるはずだ。